新能源电池创新技术与展望
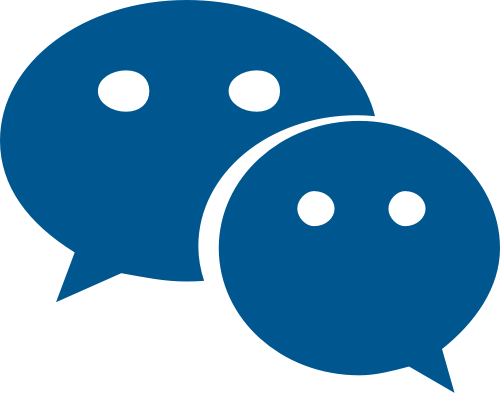
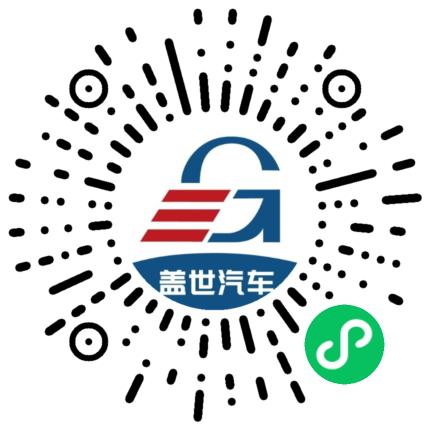
伴随着上游材料价格的不断攀升,动力电池材料的创新已是刻不容缓。目前,颇具潜能的固态电池已引起业内关注,其关键的固态电解质、正极和负极材料以及粘接剂已有多条路线正在推进中。
2022年11月17日,由盖世汽车主办,上海虹桥国际中央商务区管委会、上海闵行区人民政府指导,上海南虹桥投资开发(集团)有限公司协办的2022第二届汽车动力电池论坛上,北京理工大学机械与车辆学院、(发改委)电动车辆国家工程研究中心(设在北京理工大学) 孙立清副教授、博士(后)表示,对于新的固态电池一定要站在新的思维角度进行考虑,例如除了通过电化学反应发电,还能思考我们能否使双电层储能和电化学储能达到一致。
展望未来,孙立清博士(后)总结道,新一代的材料变革已经来临,单纯的电化学电池或许该画上句号,物理和化学融合的新材料电池将是新发展趋势,量子电池已经进入视野,高能量的电芯电池也已经进入了资本市场,更高能量密度的物理电池也已经进入视野,行业必将迎来重新洗牌。唯有重视材料技术,才能发展好新能源产业。
以下为演讲内容整理:
结构创新+材料创新双管齐下 化解电池安全难题
在过去的二十年来,电动汽车的发展经历了几个不同的阶段,尤其在近5-10年内电池的创新非常踊跃。电池的创新主要是结构方面的创新进步最快,从2019年蜂巢能源的叠片电池开始,到今年宁德时代推出麒麟电池CTP3.0,电池结构创新潮起云涌。
伴随着电池结构的创新,我们也解决了电动车上的很多核心问题。值得一提的是宁德时代从无模组发展到CTP 2.0、3.0以及麒麟电池,可以说走到了CTC的道路上。此外,特斯拉、比亚迪等汽车公司也在此方面做了很多创新。然而,电动汽车起火问题并未完全解决,甚至随着电动汽车数量的猛然提升呈现出增加趋势。目前,电动车电池的安全问题仍值得高度,需要我们从材料、结构双方向入手。
材料是人类文明的基石,在过去的发展历程当中,人类的每一次进步或技术突破都是伴随着材料学的突破开始的。到了今天,在新能源汽车电池上,大家已经吃尽了原材料价格抬升带来的苦头,因此现在的当务之急是进行材料的创新。
材料革命已经到了关键阶段,成为迫切需要创新的领域。过去国产电池受到的制约有很多,从隔膜材料的产业链上就能看出来,从隔膜核心制造装备到原材料,我们能够自给自足的不多,进口依赖严重,大大压缩了整个行业的盈利空间。除了隔膜,包括电池所用的粘接剂PVDF也有将近一半需要进口。
为改变过去依赖进口的局面,整个电池都需要材料创新。今天,固态电池作为一种颇具潜能的电池已经引起了人们的关注,除了固态电池的关键电解质,相关的正极材料和负极材料也有多条路线在推进当中。
需要强调的是,对于新的固态电池一定要站在新的思维角度进行考虑,例如除了通过电化学反应发电,还能思考我们能否使双电层储能和电化学储能达到一致。理论上,固态锂电池由于双电层效应可以储存更多电荷,也就意味着,固态锂电池的容量是普通锂电池的双倍储量。
电池技术今天在持续突飞猛进,例如号称要做硅碳纳米负极的安普瑞斯已经在国内落地,资料称利用光刻技术等技术来生产硅碳纳米负极将彻底解决硅碳负极膨胀的问题。宝马、奔驰也已经开始考虑能量密度更高的硅阳极电池,但其中也需要考虑如何解决硅膨胀的问题。目前已有企业采用石墨掺杂少部分硅的方式来提升负极容量,这可能还需进一步的改进工作以兼顾提高能量的同时做到循环寿命的提高。
我们需要进行更多的创新,因此特斯拉对于硅碳纳米线电池的期待也十分迫切。下面我将就电池材料技术为大家介绍几部分内容,包括固态电池等相关电池所带来的装备变革,以及电池系统方面的技术。
PI阳离子粘接剂
图片来源:北京理工大学机械与车辆学院、(发改委)电动车辆国家工程研究中心(设在北京理工大学) 孙立清副教授、博士(后)
PI阳离子粘接剂的优势是熔点能提高到220度以上,分子量更大,新型PI粘接剂的黏性更好。这种材料粘接剂的使用将改变目前的锂离子电池。
采用阳离子粘接剂,首先会把电池材料的种类减少至一种,即正极、负极只需要一种材料。其次,使用这种材料后就无需再使用NMP、PVDF、SBR、CMC等材料。由于NMP材料在空气中容易被氧化成过氧化物,加热这种过氧化物将十分容易产生爆炸,而NMP作为电池正负级材料使用中的稀释剂,尽管要经过烘烤环节,但最后的残留是必然的。且在产线上使用PVDF的过程当中,也不会对PVDF原材料中的过氧化物进行检测,PVDF往往会在车间和烘烤环节中重新收集起来进行再利用。就算残留在电池中的PVdF没有被氧化,电池的正极材料中也并不缺氧,只要有氧(电池正极材料不缺少氧)的存在,就会有NMP变成过氧化物,而一旦电池由于各种原因产生温升,这种过氧化物也必然会随同电解液中的有机物导致电池爆炸。
此外,由于PVdF粘接剂的分子量小,粘接强度不高,将(由于电池的“呼吸”引起的交变应力)容易引起电池的过早衰减。因此阳离子粘接剂的使用不仅能解决爆炸问题,也可以增加电池容量,以及延长电池的寿命,并能大大改善锂电池锂离子的(电场)环境。锂电池是摇椅电池,移动在正负极之间的是Li+,它会在其周围感应出负磁场,试想它在什么样的电场环境下移动更容易或者不至于出现在负极的聚集和析出呢?正极为S极还是N极,配合上负极为S极还是N极哪个配对更好呢?使用它,电池正负极仅用一种粘接剂,它能根本上改善电池的安全性,能提升容量10%左右,能改善锂离子移动的(电场)环境,提升电池寿命一倍左右。还能使材料搅拌环节节电三分之一,烘烤环节节电50%。对于富锂锰材料可将其首效由60%左右提升至99%以上。这种粘接剂的使用对整个新能源行业(包括光伏领域使用的粘接剂,更换不可小觑)的影响也会很可观。这是我们需要创新的第一种材料。
PI粘接剂作为阳离子形式的粘接剂,当与阴离子性质的GDL基体的碳纸材料共同使用时,将有利于氢质子的移动(酚醛树脂是阻碍质子移动的;而阴极性质的粘接剂会排斥碳质表面的负离子性质的需要竖立的以维持GDL的通透性的“绒毛”,使碳质的通透性降低。)。它使氢质子H+容易移动穿过扩散和更好高效地进行电化学反应,从而改善燃料电池MEA组件的性能,提高燃料电池电化学转化效率(可由目前的50%-65%提升至80%以上)。因此这种粘接剂的应用除了锂电池,也能应用于光伏太阳能、单晶硅和多晶硅,以及燃料电池双极板,可作为锂电池、钠电池、镁电池的正负极粘接剂,以及全固态锂电池、钠电池正负极的无溶剂粘接剂。
PI阳离子粘接剂也可以作为无溶剂的粘接剂,用于导电陶瓷和电磁屏蔽的粘接。
固态电解质与硅碳纳米线
固态电解质方面,目前我们已可以自主制造LGPS材料,这种材料类似早期被日本用于电动车和造船等用途的材料。2014年丰田公司就开始将类似的LGPS材料利用到硫化物固态电池上在小车上做实验。我们也可以自主制造鳞片状的NASICON型的氧化物固态电解质,其具有优良的电化学导电率,且使用它也能同时解决固态电池的界面问题。还有一种高分子固态电解质材料,它能造出稳定的耐久的和导电特性优异的固态电池界面!下面会略详细介绍。
图片来源:北京理工大学机械与车辆学院、(发改委)电动车辆国家工程研究中心(设在北京理工大学) 孙立清副教授、博士(后)
作为负极材料,除石墨、硬碳、软碳和钛酸锂以及锂金属负极外要算是硅碳纳米线负极了。对于硅碳纳米线负极,它结构有几乎完全有别于碳纳米管。如果采用光刻方式生产,成本将十分高,静电纺丝的生产方式也会在装备等方面面临“卡脖子”问题,对此我们找到了一种全新的生产方式,能更为可行地、经济地大规模生产硅碳纳米线负极。硅碳纳米线负极如果和优质的三元材料进行配合,所制造出的电池性能将会非常优异,我们也可以控制这种硅碳纳米线材料的微观参数,并将其用于钠离子电池中。
固态电池界面技术
接下来再介绍一下界面技术。中科院物理所采用的是原位固化方案,对于固态电解质和正负极材料之间的界面问题已经处理得很好了,目前我们还有更新的解决方案。
我们认为首先可以采用非生产性造膜界面电解质成膜技术,这种技术具有高度稳定的电化学界面,能降低界面阻力;其次没有液态电解液出现,不受温度时间影响,热稳定性好,能提高电池的安全性,且形成的是一体化的界面膜。这个技术彻底解决了电解质界面膜的相容性、稳定性和离子导电性问题,也解决了界面粘弹性、相容性、稳定性、离子导电性问题,离子导电性达到1x10-2S/cm~1x10-3S/cm,和液态锂盐导电性能一致。这项技术能提升整个电池的性能,目前已国外投资者关注,国内也急需建厂,且相关的知识产权也是我们中方可控的。
另外一种方案,就是采用一种新的自然界面工程物质,它是白色的,密度3.8-6.0g/ml(25度),具有层状化工物,化学稳定性较高,层状结构稳定,有较大的比表面积(物体所具有的表面积),表面电荷密度大(单位表面积上的电荷数),与有效化学反应物融合后具有离子交换功能,固体酸性。不溶于水和有机溶剂。能耐较强的酸和一定的碱度,且界面稳定性和机械强度很高。采用这种材料,在解决固态电解质问题的同时,也能解决界面问题。我们也探讨到了一种利用绝缘材料为中间层两侧粘接以具有超高导电性层状界面材料从而解决了固态电池界面问题的具有高能量密度和10-20年+的超长寿命的新材料电池。
钠电池、长寿固态电池与装备技术
多家公司已经开始投资和生产钠电池。如果在钠电池中采用硅碳纳米线负极和阳离子粘接剂,我们所做出来的电池能量密度将能达到200-260 Wh/kg。换句话说,目前用新材料做出来的钠电池已可以达到三元的水平。
钠电池有很多材料技术路线,各家有各家的优势。像振华集团做出来的产品能量密度目前为150-160Wh/kg,未来有望做到170-180Wh/kg;循环次数常温为4000+次,高温不到1000次,再过半年到一年将能做到6000-8000次;产品电压目前已实现4.0V,现在在做4.1V、4.2V的体系;低温性能上,零下20度可以实现90%+的容量保持率。快充性能为4C-5C,首次效率87%-88%,和锂电差不多。钠电池的出现可以有效缓解锂电池的紧张,钠电池目前已有许多相关的技术进展。
关于长寿命的固态电池,网上最近有一则报道称,哈佛大学的工程师研发出了能够使用100年的固态电池技术。伴随着固态电池、干式电极技术的出现,整体装备技术也发生了很大的变化。例如在干式电极中,如果采用阳离子粘接剂,由于它的黏度很高,在对电极材料进行混拌时将需要新的装置。
图片来源:北京理工大学机械与车辆学院、(发改委)电动车辆国家工程研究中心(设在北京理工大学) 孙立清副教授、博士(后)
电池系统技术及展望
在电池最后的生产过程中,特斯拉是把电解质、正极材料和负极材料都做成了薄层,最后对三层正极、负极和固态电解质材料进行贴合,所以还需要贴合机。整个电池系统的技术也在发生新的变化,因此技术的进步是非常迅速的。电池材料技术正在不断创新,新的固态电池将不再使用隔离膜、电解液、PVDF、NMP,也无需用SBR和CMC。钠电池的出现也会为锂电池提供替代,缓解目前锂电池锂资源的紧张态势,对储能行业、电动汽车行业将非常有益。
正极材料目前看来还有新的改进方式,如果采用阳离子粘接剂、硅碳纳米线负极、固态电解质,可以实现260Wh/kg的钠电池,且这种电池会比锂电池更耐低温。
这些材料也可以用于铝离子、镁离子电池。目前国内已经做了镁离子固态电池,能量密度达到400 Wh/kg。单晶石墨烯等新材料的出现,必然会为电池带来更加深入的技术性革命。如果采用富锂锰基正极材料和PI阳离子粘接剂,再采用硅碳纳米线负极,可以做出来600Wh/kg,制造出能用于特殊用途的电池并不是难事。
接下来再为大家介绍量子电池。量子电池和其他电池相比有较多优势,放电率、安全、尺寸、重量、功率密度、能量密度、自放电、循环寿命、充电性能、效率等性能都将有大幅的提升。其功率密度将达到每升10千瓦以上。目前,美国、韩国等国家已有企业在做量子电池。
电池技术正在从过去的化学储能,开始向化学和物理储能兼顾融合的方向发展,同时也在向更高能量密度的物理电池方向发展。其中参数的变化十分令人振奋。
动力电池的能量密度从260Wh/kg的钠固态负极预钠,发展到350 Wh/kg的锂阳极,再发展到(一家台湾公司做出的389 Wh/kg)锂金属负极电池;如果利用三元加上某种元素,提高分子级架构的稳定性,或采用固态和硅碳纳米线预锂,可以做到560-800Wh/kg之间的能量密度。800Wh/kg电池需综合考虑双电层物理储能+化学储能。如果采用更好的拓扑相变新材料,可以做到1000Wh/kg以上。
燃料电池由于目前电化学转化效率不高,在全周期碳排放和能量转换效率角度给了氢内燃机、甲醇内燃机以机会。如果通过阳离子粘接剂等材料使燃料电池的转化效率达到80%+,那么燃料电池一定会越内燃机,此时甲醇内燃机、氢内燃机或许就不一定再具有优势了。锂电、氢能的融合或许会有机会,但需要对动力系统技术进行提升,过去单纯的基于脉宽调制技术的动力系统技术,将需要用新的能源动力系统和控制技术解决目前车载电源和负载无法工作过程中无法强电物理隔离的问题后来进行替代。
此外,电池行业正出现超级电芯高性能电池,它的能量密度可以达到1400W/kg,放电的功率密度可以达到11kW/kg,这种电池项目也在逐渐落地中。也有一种超高能量和超长寿命的电池,这种电池的使用寿命为100年,能量密度可以达到21kWh/kg。
总结以上,电池创新仅靠结构创新是远远不够的,必须从材料创新入手。其次,老一代的材料已经到了后时代,后时代或许将持续3年至5年。新一代材料的变革已经来临,单纯的电化学电池或许将画上句号,物理和化学融合成为新材料电池的新发展趋势,量子电池已经进入视野,高能量的电芯电池也已经进入了资本市场,行业将迎来重新洗牌。因此我们一定要重视材料技术,重视材料产业,只有这样才能发展好我们国家的新能源产业。
(以上内容来自北京理工大学机械与车辆学院、(发改委)电动车辆国家工程研究中心(设在北京理工大学)的孙立清副教授、博士(后)于2022年11月17日由盖世汽车主办,上海虹桥国际中央商务区管委会、上海闵行区人民政府指导,上海南虹桥投资开发(集团)有限公司协办的2022第二届汽车动力电池论坛发表的《新能源电池创新技术与展望》主题演讲。)